Comparative Study on Machined Parts of Titanium Alloy TC4 and Stainless Steel 1Cr18Ni9Ti in China
Titanium alloy TC4 is a medium-strength α-β type two-phase titanium alloy containing 6% α stable element Al and 4% β stable element V. TC4 parts have excellent corrosion resistance, high temperature resistance and high specific strength, and are the most widely used in aerospace. The TC4 parts have a small specific gravity, high strength, and high temperature strength.
1Cr18Ni9Ti is austenitic chrome-nickel stainless steel iron. It has excellent mechanical properties, good corrosion resistance, outstanding cold deformation ability, non-magnetic properties, etc. It has been widely used in aerospace, machinery manufacturing and people's daily life.
Due to the difficulty in processing titanium alloy TC4 and stainless steel 1Cr18Ni9Ti, low cutting efficiency and fast tool wear, the two materials become typical difficult materials. The two materials differ greatly in physical, chemical and mechanical properties. Studying their processing properties, selecting suitable machining tool materials, optimizing machining geometry parameters, and improving machining efficiency are urgent problems to be solved. The comparison of the machinability analysis of titanium alloy TC4 and stainless steel 1Cr18Ni9Ti is shown in Table 1.
Based on the above comparative analysis of the machinability of the two materials. It is not difficult to find that TC4 is mainly composed of high hardness, high strength, small thermal conductivity, large elastic modulus, large chemical activity, especially high temperature strength, resulting in large cutting force; The material has poor thermal conductivity and severe friction, which is easy to cause the cutting heat on the cutting edge and the cutting edge to be very concentrated, resulting in high cutting temperature; At high temperatures, the interdiffusion of chemical elements between the tool material and the TC4 material causes diffusion wear, and the high temperature also causes chemical reaction between the tool material and the surrounding medium to cause chemical wear.
However, 1Cr18Ni9Ti is characterized by high elongation, high work hardening and affinity, so the plastic deformation in the cutting process is large and the turning force is increased. The plastic deformation of the workpiece material is large, and the friction between the workpiece and the tool is also large, and the cutting heat generated during the cutting process is high, so that the cutting temperature is high; Stainless steel has high affinity and strong adhesion, so it is easy to form chip nodules in the cutting process, which reduces the surface roughness. Hard spots formed of carbide in stainless steel exacerbate tool wear.
Therefore, the rational selection of tool materials has become the key to solving the low processing efficiency of these two materials. Tool material selection should first be the primary consideration for reducing cutting temperatures and reducing tool wear. The tool material is required to have high hardness and strength, good wear resistance and toughness, and high heat resistance. In addition, special care should be taken when selecting tool materials to avoid tool wear due to the affinity of certain elements between the tool material and the workpiece material.
Neither TC4 nor 1Cr18Ni9Ti can be processed with YT-type cemented carbide. It is necessary to select fine-grained YG-type hard alloys such as YG6, YG8, YG6X, YG6A, etc. which have small affinity with Ti element, good thermal conductivity and high strength. The tool material is selected according to the international classification of processed materials. TC4 generally selects Class S tool materials;
1Cr18Ni9Ti generally chooses M type tool materials
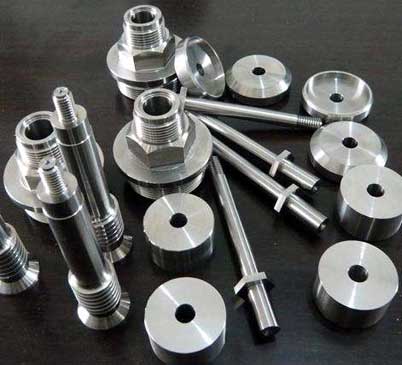
1Cr18Ni9Ti is austenitic chrome-nickel stainless steel iron. It has excellent mechanical properties, good corrosion resistance, outstanding cold deformation ability, non-magnetic properties, etc. It has been widely used in aerospace, machinery manufacturing and people's daily life.
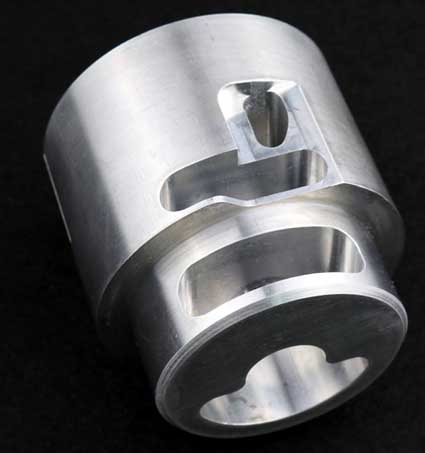
Due to the difficulty in processing titanium alloy TC4 and stainless steel 1Cr18Ni9Ti, low cutting efficiency and fast tool wear, the two materials become typical difficult materials. The two materials differ greatly in physical, chemical and mechanical properties. Studying their processing properties, selecting suitable machining tool materials, optimizing machining geometry parameters, and improving machining efficiency are urgent problems to be solved. The comparison of the machinability analysis of titanium alloy TC4 and stainless steel 1Cr18Ni9Ti is shown in Table 1.
Table 1 Comparative analysis processing TC4 titanium alloy and stainless steel cutting 1Cr18Ni9Ti
Material |
Strength and hardness Different |
Plastic deformation Different |
Thermal Conductivity Different |
Elastic Modulus Different |
active different |
TC4 | High hardness and strength, hardness 359HV, tensile strength at room temperature ≥ 895MPa |
Small elongation (10%) |
Very low thermal conductivity (7.955W/m·K) |
The modulus of elasticity is 110GPa
|
Large chemical activity
|
1Cr18Ni9Ti |
Hardness is 187HV, Tensile strength is 520MPa |
Large elongation (45%) |
Large thermal conductivity (for 16.2W/m·K) |
The modulus of elasticity is 206GPa | High work hardening and high affinity |
Based on the above comparative analysis of the machinability of the two materials. It is not difficult to find that TC4 is mainly composed of high hardness, high strength, small thermal conductivity, large elastic modulus, large chemical activity, especially high temperature strength, resulting in large cutting force; The material has poor thermal conductivity and severe friction, which is easy to cause the cutting heat on the cutting edge and the cutting edge to be very concentrated, resulting in high cutting temperature; At high temperatures, the interdiffusion of chemical elements between the tool material and the TC4 material causes diffusion wear, and the high temperature also causes chemical reaction between the tool material and the surrounding medium to cause chemical wear.
However, 1Cr18Ni9Ti is characterized by high elongation, high work hardening and affinity, so the plastic deformation in the cutting process is large and the turning force is increased. The plastic deformation of the workpiece material is large, and the friction between the workpiece and the tool is also large, and the cutting heat generated during the cutting process is high, so that the cutting temperature is high; Stainless steel has high affinity and strong adhesion, so it is easy to form chip nodules in the cutting process, which reduces the surface roughness. Hard spots formed of carbide in stainless steel exacerbate tool wear.
Therefore, the rational selection of tool materials has become the key to solving the low processing efficiency of these two materials. Tool material selection should first be the primary consideration for reducing cutting temperatures and reducing tool wear. The tool material is required to have high hardness and strength, good wear resistance and toughness, and high heat resistance. In addition, special care should be taken when selecting tool materials to avoid tool wear due to the affinity of certain elements between the tool material and the workpiece material.
Neither TC4 nor 1Cr18Ni9Ti can be processed with YT-type cemented carbide. It is necessary to select fine-grained YG-type hard alloys such as YG6, YG8, YG6X, YG6A, etc. which have small affinity with Ti element, good thermal conductivity and high strength. The tool material is selected according to the international classification of processed materials. TC4 generally selects Class S tool materials;
1Cr18Ni9Ti generally chooses M type tool materials